The role and place of contractual relations in the conditions of the food supplements market
- .
- Jul 3, 2024
- 6 min read
The contractual system is a kind of market and non-market symbiosis of an economic organization, which receives its material embodiment in a legal document (contract) regulating economic relations. The contract system cannot be separated from the general level of development not only of the economy, but also of the legal system of an individual country. Therefore, there is no general theory of contractual relations that is uniform for all countries, since each country has its own specific contractual system.
In recent years, the practice of transferring individual stages and operations of production, packaging and quality control of food supplements from the main manufacturer to subcontractors has become increasingly widespread.
Contract manufacturing (CM) is the production of products to order at the facilities of an independent manufacturer, which ensures complete preservation of the technological cycle and quality control of finished products in accordance with the customer's requirements. It is developing as fast as the food supplement market. Mergers of companies, which are now more frequent, mean that their production policies are also changing. The main factor in the development of contract production, as a special sector of the food additives market, is the increase in the price of scientific research. By getting rid of production costs, companies could direct more money to creating new supplements. Contract manufacturing increases the globalization of the nutritional supplement market, since the main customers are multinational corporations, which can transfer to contact manufacturers not only the position of their product "line" and the corresponding technology, but also the quality assurance strategy.
A contract manufacturer is a company that fulfills orders for the production of products under someone else's trademark. There are also companies on the market of nutritional supplements that:
• have a fairly large "portfolio" of products, but they do a better job of promoting them than producing them;
• knows how to track promising novelties and attract them to his "portfolio", while being a mediocre producer;
• focused on the development and promotion of bad products to the market;
• are able to establish a production cycle with the appropriate quality and the required volume of production.

Today, there are 10-20 large contract manufacturers in the world. The average annual volume of leading companies is up to $200 billion. And they hold a significant share of the global market. Along with the leading companies, there are medium and small contracting firms, their number is not exactly known (approximately 900).
The following types of contract manufacturers are distinguished:
• Contract Manufacturer (CM) – a company that produces components or finished products for another customer company;
• Original Equipment Manufacturer (OEM) – a customer company that is usually focused on development and sales and is called an original equipment manufacturer;
• Original Design Manufacturer (ODM) – companies that provide manufacturing services under the customer's brand.
The situation in the field of contract production of food supplements began to change radically in connection with the movement of "GMP-ization" of enterprises (GMP-certified factories with modern equipment, appropriate classes of cleanliness of production premises, etc. appeared). .) Enterprises that are unable to ensure the proper quality or volume of bad production at their own facilities will be forced to choose manufacturing partners

As a rule, companies prefer to work with a limited number of contract manufacturers (an average of six manufacturers).
Demand for contract manufacturing services is growing. This is facilitated by a number of circumstances, in particular, the fact that productions that were previously located in the urban area are being moved beyond its borders. Enterprises that do not have sufficient resources (or strategic motivation) to deploy modern production in a new city tend to look for contract partners.
A level 1 contract is:
Agreement on production - contains the subject of the agreement, terms of performance and settlement procedure.
Service Level Agreement or Packaging Agreement.
Tier 1 deals apply to Tier 2 deals:
• Quality agreement - an integral part of interrelated agreements covering aspects of GMP, quality management (QM), quality control (QC);
• Supply agreement - covers aspects related to terms of supply, planning (eg production planning by the subcontractor), confidentiality and other specific aspects.
They are very different in their specifics, therefore, in order to avoid difficulties in development and coordination, they are separated into separate documents and linked to each other by cross-reference.
All risks related to the quality of the products during the stages of contract manufacturing must be analyzed and outlined in the Quality Agreement before the agreement is signed between the manufacturer and the customer.
At the stage of forming the quality agreement, prerequisites for the validation of the technological process must be created. The contract itself must clearly describe the planning and verification of the contractual technological process (stages).
The contract must be conditioned by the management capabilities of the business process, which is transferred to contractual execution.
For the execution of the contract, a group is created consisting of the management staff of the customer's organization and the executor's organization. During the entire term of the contract, he must regularly exchange information.
A contract manager must also be appointed. At the stage of developing the contract, it is necessary to separate the spheres of responsibility of the customer and the contractor.
STAGES OF CONTRACT PRODUCTION OF FOOD SUPPLEMENTS
I Search for the Executor under the contract, conducting negotiations
II Calculation of the technical and economic feasibility study (TEO)
III Analysis of information and selection of the Contractor
IV Risk assessment, evaluation of the quality management system, conducting an audit of the Contractor. (Quality Management-QM)
V Organization of research and industrial approval (DPA)
VI Conclusion of the DPA contract VII Final decision on the selection of the Executor
VIII Conclusion of commercial agreements on production
IX Conclusion of technical agreements
X Conclusion of agreements on storage of products
XI Supervision of the subcontractor
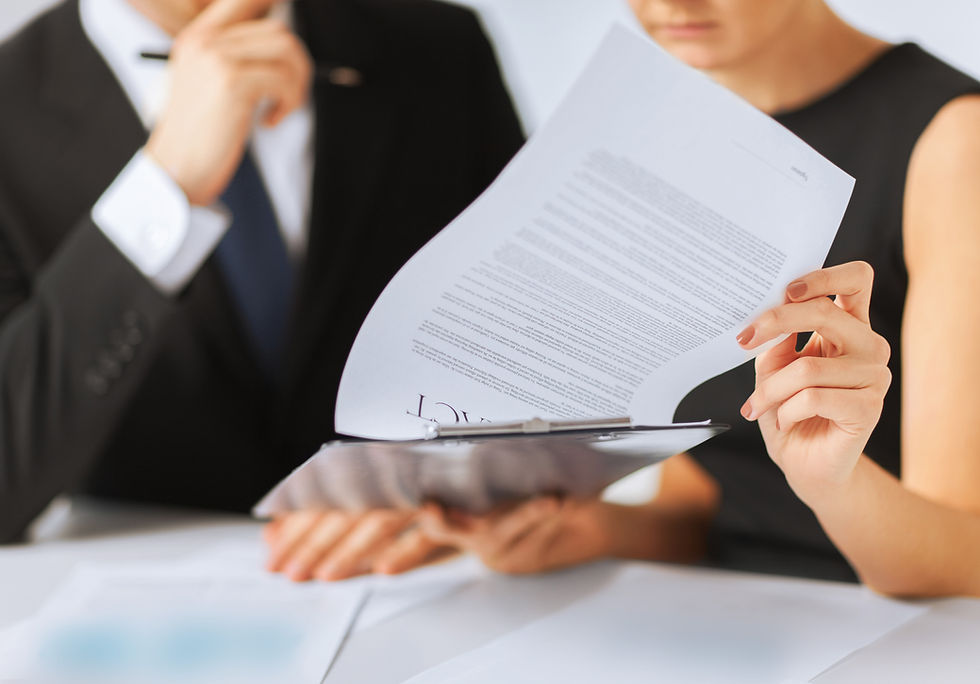
As can be seen from the data in the above list, even if a company has good manufacturing practice (GMP) but has large production volumes, it may order some nutritional supplements to expand sales. Such a company can enter into a contract for both additive manufacturing and secondary packaging, depending on its strengths and weaknesses.
If we evaluate the profitability of different types of contract manufacturing services (full cycle, packaging of products supplied in bulk, secondary packaging), then, at first glance, it should be the highest in full cycle production, but at the same time it is necessary to take into account who is the supplier of substances, auxiliary substances and packaging materials. At this stage of the development of contact production of bads, packaging of products in bulk and secondary packaging is in greater demand. A complete cycle is not always possible from the point of view of the production capacities available at the enterprise (equipment, production conditions, etc.). When packing products supplied in bulk, the manufacturer is obliged to fulfill only the requirements for packaging equipment and packaging materials. The majority of factories go the way of providing contract manufacturing services from packaging, since in this case the term of registration of a food supplements is much shorter than when registering a full cycle. With any model of contract production, the main thing is that the maximum profitability is achieved through the optimal use of all production capacities, the use of all production reserves, since the profitability of contract production itself is low and amounts to 15-25%.
According to the latest reports by Visiongain, the food supplement contract manufacturing market was valued at USD 143.0 billion in 2023 and is projected to grow at a CAGR of 10.3% during the period 2023 to 2033..
The main factors contributing to the growth are the expiration of patents and increased demand for generic supplements, as well as investments in research and development in this field.
Thus, we can expect an increase in the volume of contract production of food additives in the coming years.
In summary, it can be said that contractual relations in the production of food additives are quite a common phenomenon, which allows the customer to save funds for the development of production, receive a finished product with a strictly fixed cost and focus on its promotion, and can also become an effective tool for the implementation of scientific and technical, innovative and socio-economic programs, in particular, providing the population with affordable vital medicines and food supplements.